Optimal Fatigue
Strength
Compound Layer Free
Low Temperature treatment without loss
of corrosion resistance for high chromium
alloyed steels
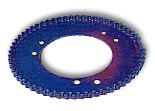 |
Timing Gears
StE4
Depth >0, 4 mm
|
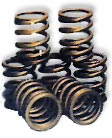 |
Valve Springs
50CrV4
Depth >0, 15 mm
|
|
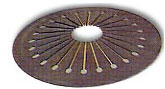 |
Plate Springs
55MnSi7
Depth >0, 15 mm
|
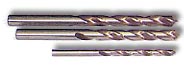 |
Drills
S6-5-2
Depth 5-10 mm
|
 |
 |
|
- Ejectors
- Pison Rods
- Valves
- Cutting Tools
- Stamping Tools/
Bending Tools
- Punching Tools
|
|
|
 |
 |
|
Super Hardness
Compound Layer Free Plus PACVD
|
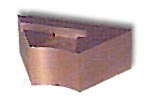 |
Cutting Tools
S6-5-2
3 mmTIN
|
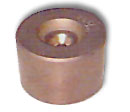 |
Forging Dies
X155CrVMo12.1
4 mmTIN
|
|
 |
 |
|
- Gears
- Extrusion Dies
- Aluminum Die
Castings
- Plastic Moulds
|
|
|
 |
 |
|
Ductile and
Wear Resistant
|
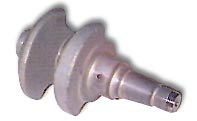 |
Crankshafts
34CrV4
Depth > 0, 25 mm
|
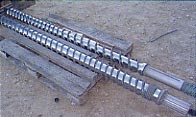 |
Extrusion Worms
31CrMoV9
Depth > 0, 5 mm
|
|
Gears
14CrMoV6.9
Depth > 0,5 mm
|
|
Aluminum Die Casting
X38CrMoV5.1
Depth > 0,2 mm
|
|
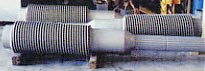 |
Driving Mills
42CrMo4
Depth > 0, 4 mm
|
|
Forging Tools
X38CrMoV5.1
Depth > 0,2 mm
|
|
Plastic Moulds
40CrMoV5.1
Depth > 0,2
|
 |
 |
|
- Aluminum Extrusion
Dies
- Slides
- Tools
- Pump Parts
- Glass Moulds
- Machine Parts
|
|
|
 |
 |
|
Wear and Corrosion
Resistant
|
|
Automatic Gear Box
Parts
Compound Layer:
9 +/- 3 mm
|
|
Camshafts
Cast Iron, Surface Remelted
Compound Layer:
8-10 mm
|
|
Connecting Rods
SINT D30
Compound Layer:
10-15 mm
|
|
|
Piston Rods
42CrMo4
Compound Layer:
> 10 mm
|
|
Gas Spring Tubes
Compound Layer:
5 mm
|
 |
 |
|
- Guidings
- Hydraulic Components
- P/M Parts
|
|
|
 |
 |
|
Optimal
Corrosion Resistance, Decorative
|
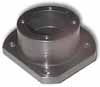 |
Bushings
C 45
Compound Layer:
> 10 mm
Oxide Layer ca. 2 mm
|
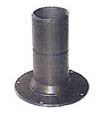 |
Cylinders
Cast Iron
Compound Layer:
>10 mm
Oxide Layer ca. 2 mm
|
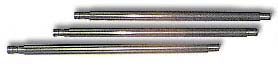 |
Piston
Rods
C 45
Compound Layer:
15-20 mm
Oxide Layer ca. 2 mm
|
|
 |
 |
|
- Tool Holders
- Hydraulic Components
- Drills
|
|
|
 |
 |
|
Industries Served
High Performance Automotive: Nascar, Formula
1, and Indy
Surface hardening in all sectors of the
metal industry
Surface hardening is required in many sectors
of the metals industry for manufactured
parts, and for production tooling.
Plasma nitriding can extend the operating
life of many products by increasing their
superficial hardness and wear resistance
and by improving their corrosion resistance
and fatigue strength. In fact, the successful
application of many products is possible
only after plasma nitriding.
Not Everything that hardens is good
Many older methods are suit being employed
for surface hardening. Some are better
than others - but all methods have some
distinct disadvantages.
- Results are not always reproducible.
- Compound zone chemistry is not controllable.
- Critical work piece dimensions are changed.
- Energy consumption is high.
- Explosive gas mixtures are required.
- Heat treatment materials are toxic.
- The process is environmentally polluting.
Many manufacturers are forced to send their
work to highly specialized commercial heat
treaters because of these problems.
Plasma nitridinga ray of hope
Very good results can be dependably obtained
with plasma nitriding. The metallurgy of
the hardened layers can be selected to consistently
meet the requirements of any specific application.
The equipment can operate at low energy
levels, with inherently safe gas mixtures
and without any danger of environmental pollution.
In spite of these important advantages
there are still some operating considerations
that have limited the general acceptance
of this process. For example, the treatment
temperature generally depends upon the proper
selection of a large number of operating
parameters like nitriding temperature and
time, gas pressure and gas mixture composition
and the plasma voltage. The proper arrangement
of the work pieces within the furnace has
required considerable operating experience.
If the work pieces were not properly arranged,
some surfaces were not nitrided or they
may have been overheated.
Until recently, plasma nitriding has been
a job for a few experts. Even with their
specialized knowledge, they were not always
able to avoid extended experiments to develop
empirical processing data before they could
reliably heat treat complicated work pieces.
ELTROPULS plasma nitriding process offers
new possibilities
These problems have been overcome with
the ELTROPULS plasma nitriding process.
With this process, the range for application
has been greatly enlarged and operating
costs have been significantly reduced. ELTROPULS
has been the right choice, even for small
companies.
The ELTROPULS process offers you
these important advantages for surface
treatment.
- Microprocessor control permits
auto matic unattended operation.
- The equipment operates without
pollution and with no undesirable
environmental impact.
- The equipment makes no demand
on plant utilities during idle periods.
- The electrical energy, cooling
water and process gas consumption
are significantly lowered because
of shorter treatment times.
- Factory assembly of the equipment,
with interconnecting wiring and
piping, limits floor space requirements
and reduces installation costs.
|
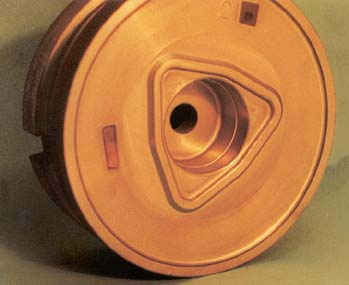
In a large forging plant,
ELTROPULS plasma nitriding has been
established as the standard treatment
for dies. A comparison with
their previous salt bath operation
showed a lot of new advantages.
The nitriding operation is less expensive
and it is now environmentally friendly.
Die life has been increased by 70%.
The furnace is able to nitride up
to 3000 lbs of these dies every day,
on demand.
|
A wide range of permissible heat treating
parameters reduces capital equipment costs
- The composition and thickness of the
compound zone are adjustable. The depth
and hardness of the diffusion zone can
be separately controlled. A wide range
of treatment temperatures permits complete
control over final metallurgical results.
- A large variety of work geometries can
be reproducibly treated without restrictive
charging limitation. Treatment of a wide
range of work sizes at one time, permits
higher throughput and better equipment
utilization.
- There is no degradation of the work
piece surfaces by arcing or overheating.
Soft spots from insufficient plasma coverage
are completely prevented. Areas that must
not be treated are easily masked.
- Tempering, stress relieving, aging and
other heat treatments can be accomplished
in the same furnace.
Advantages for your product
The ELTROPULS plasma nitriding process
gives your product the surface layer it
needs.
- a mono phased, highly ductile gamma
prime compound layer can be produced for
high strength.
- A relatively thick epsilon compound
zone can be obtained for abrasive or corrosive
application conditions.
- The formation of a compound layer can
be completely suppressed for work pieces
subject to high dynamic stresses.
- A wide variety of complex geometries
including drills and reamers, punching,
forging and extrusion dies, crankshafts
and camshafts can be uniformly nitrided.
- Chrome nickel steels can be nitrided
without separate depassivation steps.
- Changes in work dimensions and surface
roughness are minimal and in most cases
the work can be completely finished, at
lower cost in its softer state, before
nitriding.
Examples of successful applications of
the ELTROPULS process
The ELTROPULS equipment is now used worldwide
in the automotive, machine tool and manufacturing
industries to improve surface characteristics,
to solve application problems, to increase
heat treating productivity and to reduce
manufacturing costs. The examples below
show just a few manufactured parts that
are being routinely plasma nitrided.
Components of the ELTROPULS unit
- An insulated, electrically heated furnace
produces temperatures to 1200° F.
- A mechanical pump produces vacuum levels
between 50 microns and 5 torr.
- A microprocessor, permits keyboard or
menu process-parameter entry, controls
the process and provides complete documentation.
Programming the ELTROPULS Microprocessor
Nitriding parameters, including temperature
and time can be easily entered through the
keyboard in response to clear-text prompts.
A variety of nitriding programs, either
developed by the operator or supplied by
ELTRO, can be permanently stored by the
microprocessor. The furnace operator
can then start each nitriding program with
a single pushbutton.
Operation of an ELTROPULS unit
The work pieces to be nitrided are either suspended from a fixture
or placed directly on the furnace hearth.
The pumping system produces the programmed
vacuum level and the work pieces are then
heated to the proper temperature for surface
treatment. The gas composition, the
gas pressure and the temperature determine
what type of surface treatment will take
place.
A pulsed voltage is applied between the work pieces and the
furnace wall. This voltage accelerates
electrons to very high velocities (in this
special case, very high velocities are functionally
equivalent to very high temperatures) permitting
them to ionize and activate normally inert
gases like nitrogen so that the specified
surface treatement can take place.
The high energy, but thermally low temperature,
ionized gas mixture is called the plasma.
The high electron energy in the plasma permits
physical and chemical reactions to take
place that would normally require much higher
surface temperatures. The ELTROPULS
system allows the temperature of the work
pieces and the surrounding inert gas to
remain relatively low during the entire
surface treatment so the work pieces can
retain their original core properties.
|